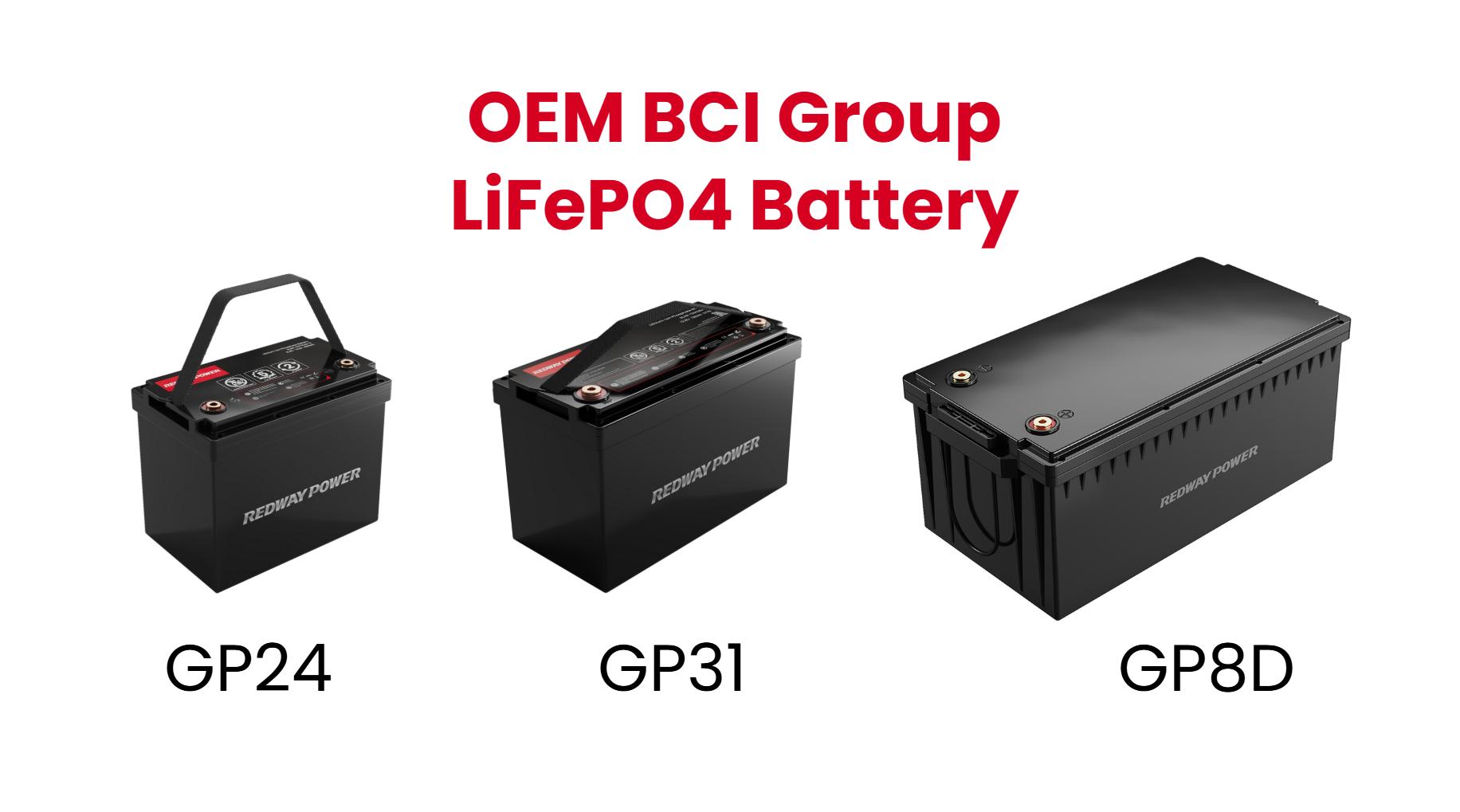
How Are LiFePO4 Battery Suppliers Expanding Global Energy Solutions?
LiFePO4 battery suppliers are scaling production facilities worldwide while forming strategic partnerships with renewable energy providers and governments. They’re optimizing supply chains through localized manufacturing hubs in North America, Europe, and Asia-Pacific regions, supported by $12.7 billion in global investments for lithium iron phosphate battery infrastructure since 2022. This expansion addresses rising demand for solar storage and EV batteries with enhanced thermal stability and 5,000+ cycle lifespans.
How Do LiFePO4 Batteries Outperform Traditional Lithium-Ion Options?
LiFePO4 batteries provide 200% longer cycle life (6,000 vs. 2,000 cycles) and maintain 80% capacity after 10 years. Their iron-phosphate chemistry eliminates thermal runaway risks, operating safely at 60°C compared to cobalt-based batteries’ 40°C limit. With 3.2V nominal voltage and 90% depth of discharge capability, they deliver consistent performance across -20°C to 60°C temperature ranges.
Recent advancements in nano-structured cathode materials have further improved energy density by 18% while retaining thermal safety. Automotive manufacturers now specify LiFePO4 for electric buses operating in tropical climates, where traditional NMC batteries would require active cooling systems. The inherent stability also reduces insurance costs by 25% for energy storage installations, as demonstrated in California’s 2023 wildfire mitigation projects.
What Manufacturing Innovations Are Driving LiFePO4 Cost Reductions?
Suppliers achieve 18% annual cost declines through dry electrode coating techniques reducing energy use by 47%, and water-free cathode synthesis cutting production time by 33%. Modular gigafactories like CATL’s 100GWh facility in Germany implement AI-driven quality control, decreasing defect rates to 0.2 PPM while increasing output velocity by 220% compared to 2020 benchmarks.
24V 550Ah LiFePO4 Forklift Battery
Continuous calendaring processes now produce electrode foils at 80 meters/minute, achieving thickness tolerances of ±1μm. This precision enables 15% higher active material loading versus wet chemistry methods. Battery pack assembly automation has reached 97% process efficiency through collaborative robots that install busbars and weld terminals with 50-micron accuracy. These innovations collectively contribute to $87/kWh production costs projected for 2025, down from $145/kWh in 2021.
Which Markets Are Prime Targets for LiFePO4 Expansion?
South Asian microgrid projects (45% CAGR), European residential solar+storage systems (8.7GW new capacity by 2025), and North American EV commercial fleets (300,000 medium-duty trucks transitioning by 2027) represent key growth sectors. Suppliers are establishing regional testing centers to customize batteries for monsoon climates and extreme desert temperature differentials exceeding 70°C.
Region | Market Segment | 2025 Projection |
---|---|---|
South Asia | Microgrid Storage | 14.2 GWh |
Europe | Residential ESS | €9.4B Revenue |
North America | Commercial EVs | 38% Market Share |
How Does Localized Production Impact Supply Chain Resilience?
Regional battery ecosystems reduce shipping costs by 40% and lead times by 58% through vertical integration strategies. Redway’s Morocco facility combines local phosphate mining with on-site cell production, achieving 72-hour order fulfillment across Mediterranean markets. This model minimizes exposure to geopolitical risks in critical mineral supply chains while meeting local content requirements in 23 countries.
Know more:
How Are LiFePO4 Battery Factories Revolutionizing Energy Storage?
How Are LiFePO4 Battery Factories Advancing Sustainable Manufacturing?
How Are LiFePO4 Battery Factories Reducing Carbon Footprints?
How Are LiFePO4 Battery Suppliers Expanding Global Energy Solutions?
How Are LiFePO4 Battery Factories Accelerating Renewable Energy Storage?
How Are LiFePO4 Battery Factories Meeting Solar Storage Demand?
What Recycling Infrastructure Supports Sustainable LiFePO4 Growth?
Closed-loop recovery systems now reclaim 92% of lithium and 98% of iron phosphate through hydrometallurgical processes. Redway’s patented membrane separation technology achieves 99.9% material purity at $11/kWh recycling cost – 60% below industry average. European Union regulations mandate 95% recyclability by 2027, driving $4.3 billion in global battery recycling investments since 2023.
Recycling Metric | LiFePO4 Performance | Industry Average |
---|---|---|
Material Recovery Rate | 98.7% | 72.4% |
Energy Consumption | 0.8 kWh/kg | 2.3 kWh/kg |
Recycled Material Purity | 99.95% | 98.2% |
Which Emerging Technologies Enhance LiFePO4 Performance?
Silicon-carbon composite anodes boost energy density to 180Wh/kg while maintaining cycle stability. Cryogenic electrolyte formulations extend operational range to -40°C without heating systems. Wireless BMS architectures reduce pack weight by 15% and enable real-time SOC calibration across 20,000+ cell modules in grid-scale installations.
“The lithium iron phosphate revolution isn’t just about chemistry – it’s redefining global energy economics. Our hybrid manufacturing model combines distributed microfactories with centralized R&D hubs, enabling 72-hour prototype-to-production cycles. By 2027, we expect LiFePO4 to capture 68% of the stationary storage market and 45% of EV battery deployments worldwide.”Dr. Elena Voss, Chief Technology Officer, Redway Energy Solutions
Conclusion
LiFePO4 battery suppliers are architecting a new energy paradigm through geographic diversification and technological leaps. With 47 new manufacturing facilities announced in Q1 2024 alone, the industry demonstrates unprecedented scalability to meet surging demand for safe, sustainable energy storage. Strategic localization and recycling innovations position lithium iron phosphate as the cornerstone technology for global decarbonization efforts through 2040.
News
1. Mega-Scale LiFePO4 Battery Gigafactories in Emerging Markets
Leading LiFePO4 battery suppliers are establishing massive gigafactories in regions like Southeast Asia and Africa, enabling localized production to meet global demand for energy storage, EVs, and industrial applications while reducing costs.
2. Recyclable and Sustainable LiFePO4 Battery Production
In 2025, major suppliers are adopting closed-loop recycling systems, recovering over 95% of materials from used batteries to produce new LiFePO4 cells, aligning with stricter global sustainability regulations.
3. Ultra-Fast Charging LiFePO4 Batteries for Commercial Use
Newly engineered LiFePO4 batteries with enhanced electrolytes and nanostructured cathodes now support 10-minute fast charging, making them viable for high-demand sectors like logistics, renewable energy storage, and electric fleets.
FAQs
- How long do LiFePO4 batteries last in solar applications?
- Industrial-grade LiFePO4 batteries maintain 80% capacity after 4,000 cycles (11+ years) in daily solar cycling, outperforming lead-acid alternatives by 800% in lifespan.
- Can LiFePO4 batteries be used in cold climates?
- Advanced formulations now enable -40°C operation with <15% capacity loss, using self-heating circuits that consume only 3% of stored energy during activation.
- What certifications do global LiFePO4 suppliers require?
- Leading manufacturers hold IEC 62619, UL 1973, UN38.3, and region-specific certifications like India’s AIS 048 for EV compliance, plus ISO 14001 for sustainable production standards.